I am so excited to be adding a new project today. It has been quite a while since my last project and I am happy to be able to share something new with you.
Recently, I was inspired by history and found some great historical projects that I wanted to make.
The first was a rag doll. Rag dolls are so easy! The body of the doll is created by tying together strips of fabric. The accessories can be sewn or not sewn depending on your preference.
Rag Doll with Sewn Accessories
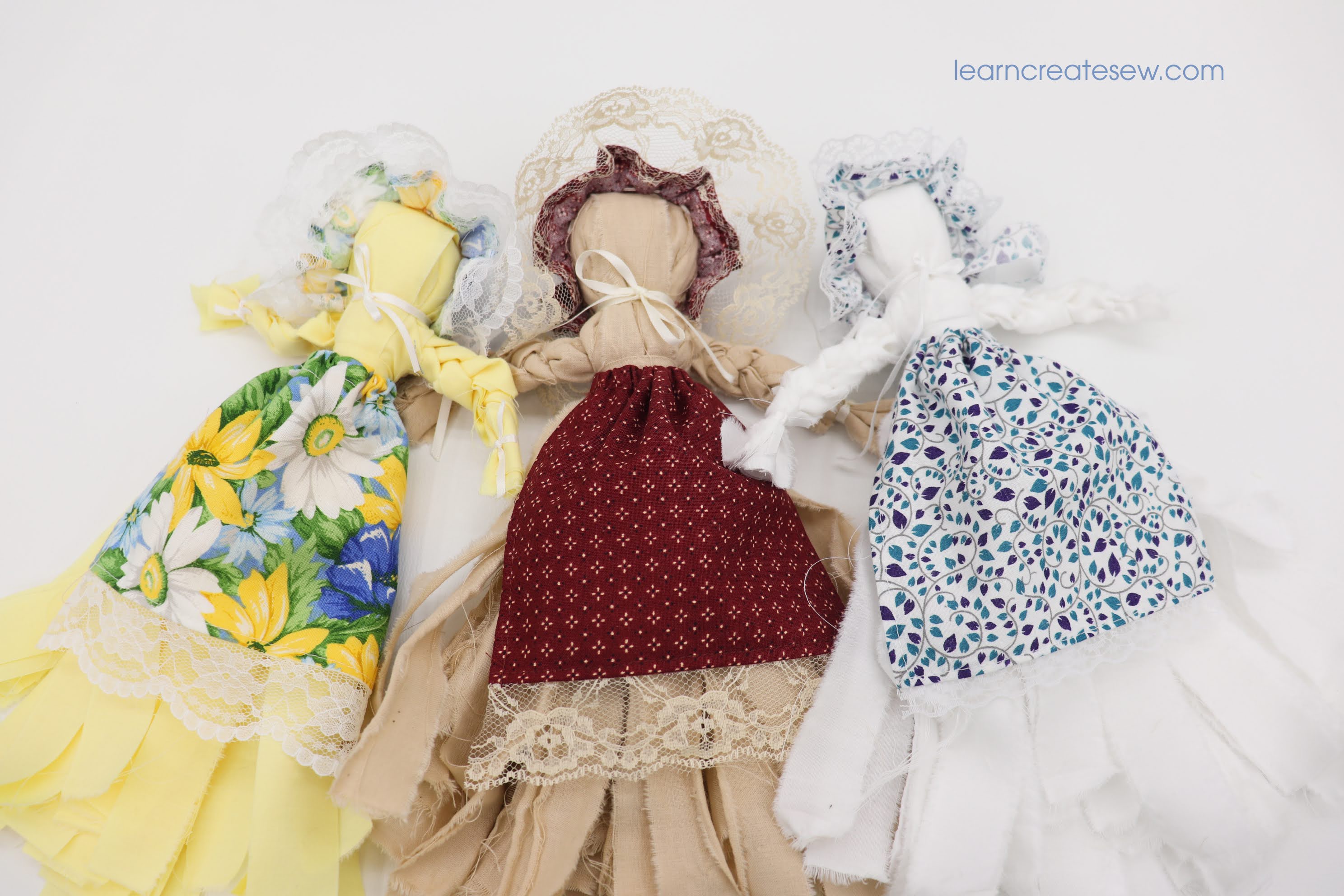
The bonnet and apron are stitched to add lace trim, finish the edges, create gathers, and make casings. I used flat lace trim, but you can use pre-gathered lace as well. The yellow and white dolls above were made using cotton/poly broadcloth and 3 cotton balls for the head. The doll below was made from dyed muslin and used 4 cotton balls to create the head. The muslin doll is a bit fuller and softer.



Each doll was made by ripping or cutting the fabric into strips arranged in a spiral, or wheel pattern, with the strips aligned at the center. Ties, either ribbon or fabric, are used to create the doll.

The doll will have a different texture depending on if you rip or cut the strips. The white and tan dolls were created with ripped strips, while with the yellow doll, the strips were cut using a ruler and a rotary color. The effect is a bit different. The ripped dolls are much softer and appear more rustic. They will all fray eventually since the fabric is not finished, but the ripped dolls have a lot more fraying to start.

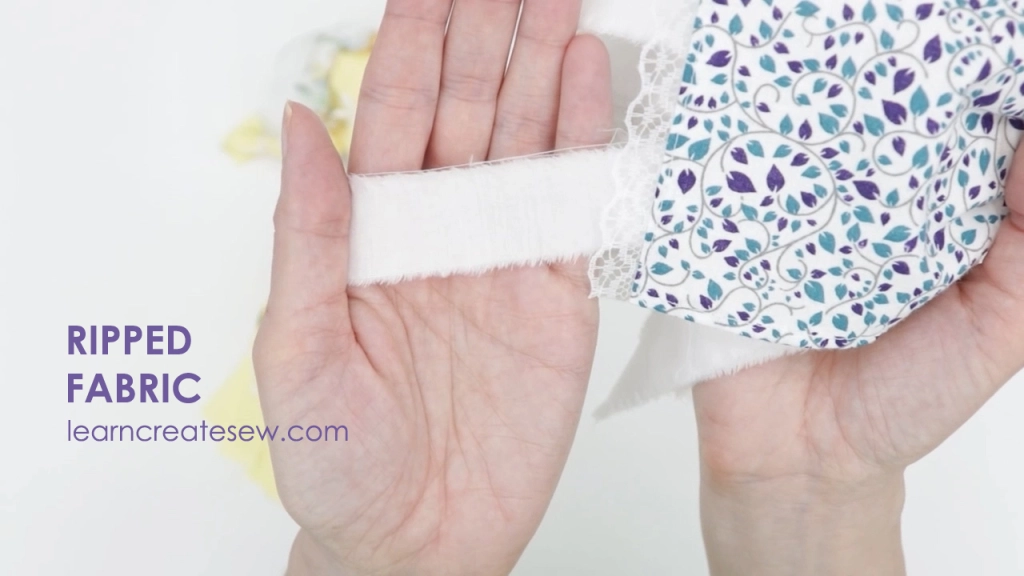
Free Pattern:
Supplies:
- 1/2 yard cotton fabric for body
- 6 x 12 inches of fabric for the accessories
- 2/3 yard of lace trim (optional)
- 1 1/4 yard satin ribbon (1/8 inch wide)
- Cotton Balls or poly-fil
The dolls do not stand on their own, so if you are interested, here are the doll stands that I used.
Detailed Instructions:
Quick Overview:
No- Sew Rag Doll
The No-Sew Rag Doll is a great option if you are making the project with small children or if you need a faster construction time.
The process is very similar, but the style is slightly different.
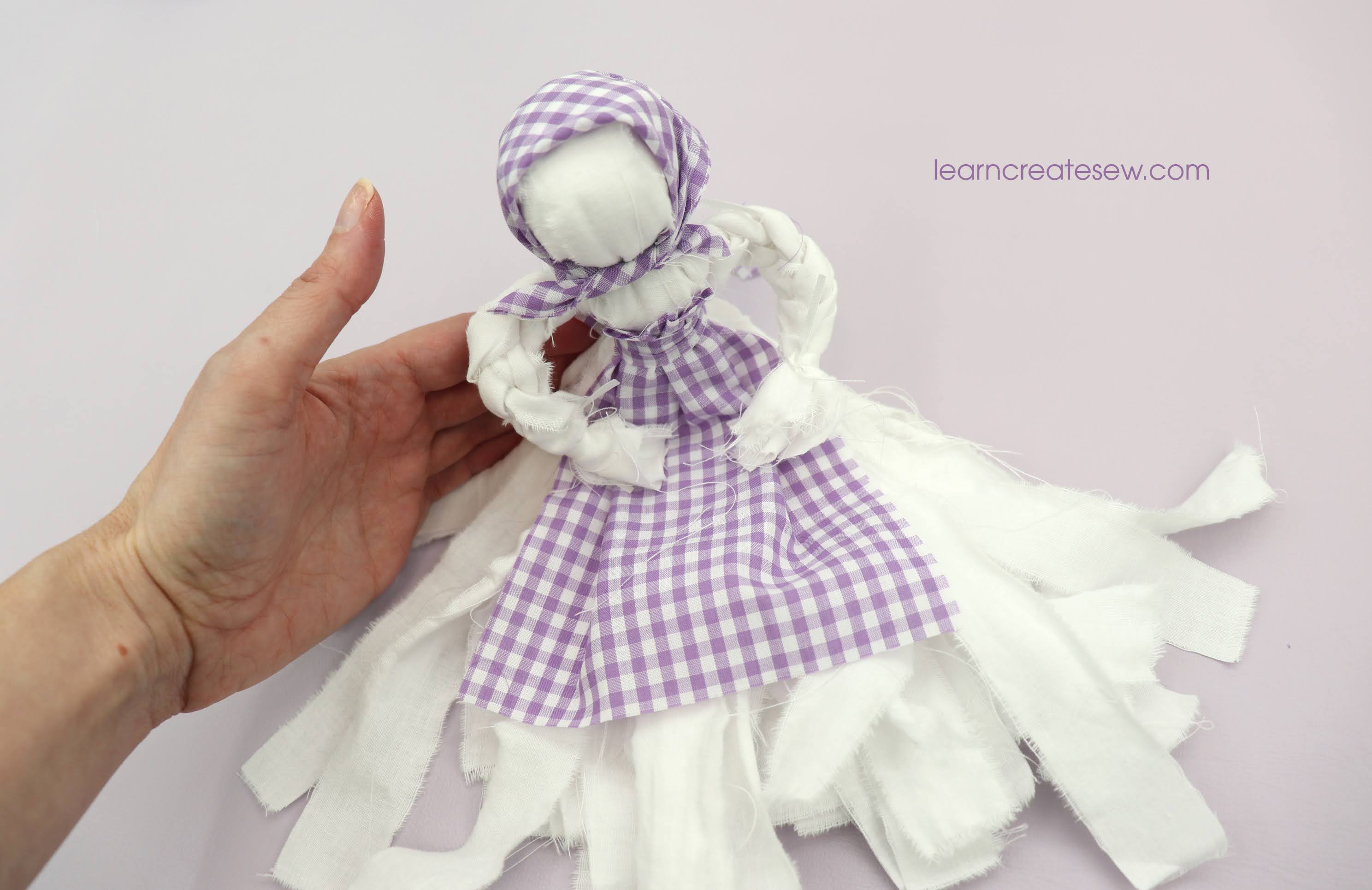
The No-Sew Rag Doll has a kerchief instead of a bonnet, and the apron is simply tied on.
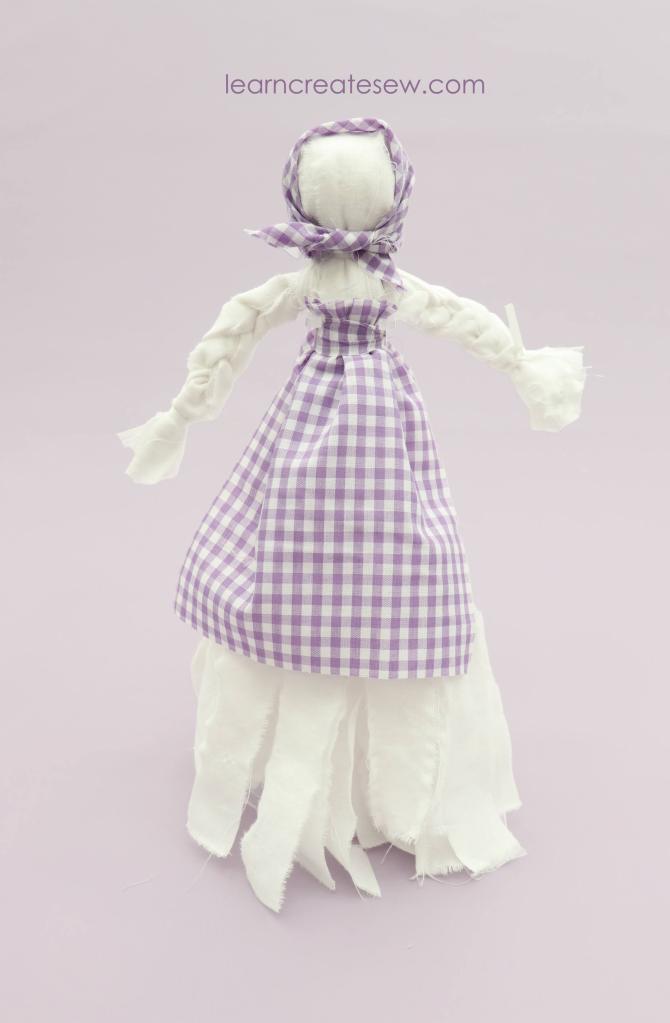


Free Pattern:
Supplies:
- 1/2 yard cotton fabric for body
- 6 x 12 inches of fabric for the accessories
- 3/4 – 1 1/4 yard satin ribbon (1/8 inch wide)
- Cotton Balls or poly-fil
The dolls do not stand on their own, so if you are interested, here are the doll stands that I used.
Detailed Instructions:
Quick Overview:
Happy Sewing…or No-Sewing 🙂